Finish Trades
The Finish Trades section, which constitutes 19% of the California General B Licensing Exam, covers a variety of final construction tasks that bring a project to completion with an emphasis on both aesthetics and functionality. This section includes the application of paint, stains, and coatings, as well as the installation of tile, stone, flooring, cabinetry, millwork, drywall, plaster, ceilings, windows, skylights, doors, and landscaping elements. Each of these tasks requires meticulous preparation, precision in execution, and adherence to safety and environmental standards. Mastery of these finish trades ensures a polished, durable result that meets both the client's expectations and regulatory requirements.
Painting, staining, coating, and interior wall Covering
Preparation and Surface Cleaning
Before any painting, staining, or coating, surfaces must be properly prepared and cleaned to ensure the best adhesion and finish. This includes removing old paint, sanding rough areas, filling holes and cracks, and ensuring the surface is dry and free of dust and debris. For best results, follow the manufacturer’s guidelines for surface preparation and cleaning products.
Painting
When painting interior walls, use paint appropriate for the specific room and conditions. For example, use high-moisture-resistant paint in bathrooms and kitchens. Paint should be applied in even coats, allowing each layer to dry completely before applying the next. Ventilate the area properly to expedite drying and reduce inhalation of fumes.
Staining
Staining is used to enhance the natural beauty of wood surfaces. Before applying stain, sand the wood smoothly and clean it thoroughly. Apply the stain evenly with a brush or cloth, following the wood grain, and allow it to penetrate before wiping off any excess. Finish with a clear protective coat to seal the stain and protect the wood.
Coating
Coating refers to various protective and decorative finishes applied to surfaces. This can include clear coatings, like polyurethane for wood, or colored coatings, like epoxy for concrete floors. Coatings should be applied in thin, even layers and allowed to cure fully between applications. Always follow the manufacturer’s recommendations for mixing, application, and curing times.
Interior Wall Coverings
Interior wall coverings can include wallpaper, fabric, or other materials applied to walls. Proper preparation is crucial, including cleaning and smoothing the wall surface. Adhesives should be chosen based on the type of covering material and wall surface. Apply coverings carefully to avoid bubbles and ensure a smooth, even finish.
Environmental and Safety Considerations
When working with paints, stains, and coatings, it is important to consider environmental and safety factors. Use low-VOC (volatile organic compounds) products when possible to reduce harmful emissions. Ensure adequate ventilation during application and drying times. Wear protective gear, such as gloves and masks, to protect against fumes and skin contact. Dispose of any leftover materials and cleaning solvents according to local regulations to minimize environmental impact.
Tile and Stone
Tile and Stone Installation
Tile and stone should be installed according to the manufacturer’s instructions and industry standards to ensure durability and proper performance. Surfaces must be prepared by cleaning, leveling, and applying a suitable substrate or underlayment. Use the appropriate adhesives and grouts for the specific type of tile or stone being installed.
Surface Preparation
Proper surface preparation is critical for successful tile and stone installation. This includes cleaning the surface of dust, grease, and other contaminants. For floors, ensure that the subfloor is level, dry, and structurally sound. For walls, a suitable backer board or waterproof membrane may be necessary to provide a stable and moisture-resistant base.
Adhesives and Grouts
The choice of adhesive and grout is essential for the longevity of the tile or stone installation. Use thin-set mortar or mastic for adhesive, depending on the tile type and installation area. Grout should be chosen based on the tile's location; for example, use epoxy grout for areas exposed to moisture, such as showers and kitchen backsplashes. Follow manufacturer’s instructions for mixing, application, and curing times.
Tile and Stone Cutting
Accurate cutting of tiles and stones is crucial for a professional finish. Use appropriate tools such as tile cutters, wet saws, and nippers to achieve precise cuts. Always wear safety gear, including goggles and gloves, when cutting tile and stone to protect against dust and sharp edges.
Waterproofing and Sealing
For installations in wet areas, such as bathrooms and kitchens, waterproofing is essential. Apply a waterproof membrane or barrier on the substrate before tiling. After installation, seal porous tiles and stone surfaces with an appropriate sealer to prevent water penetration and staining. Seal grout lines to enhance their durability and resistance to moisture.
Expansion Joints
In larger installations, it is important to include expansion joints to accommodate movement and prevent cracking. Follow guidelines for the placement and spacing of expansion joints, particularly in areas subject to temperature fluctuations or substrate movement. Use flexible sealant in expansion joints to maintain a watertight seal.
Environmental and Safety Considerations
When working with tile and stone, consider environmental and safety factors. Use dust control methods, such as wet cutting and vacuum dust collection, to minimize airborne particles. Choose low-VOC adhesives and grouts to reduce harmful emissions. Ensure proper ventilation during installation and curing times. Wear appropriate personal protective equipment (PPE), including gloves, eye protection, and dust masks. Dispose of waste materials according to local regulations to minimize environmental impact.
Floor Covering
Floor Covering Installation
Floor coverings must be installed in accordance with the manufacturer's instructions and industry standards to ensure proper performance and longevity. Types of floor coverings include carpet, vinyl, laminate, hardwood, and tile. Each type requires specific preparation, adhesives, and installation techniques.
Surface Preparation
Proper surface preparation is critical for all types of floor coverings. The subfloor must be clean, dry, level, and structurally sound. Remove any old flooring, debris, and contaminants. Address any moisture issues, as excess moisture can compromise the adhesive and the floor covering. Use a moisture barrier where necessary, especially on concrete subfloors.
Carpet Installation
Carpet installation involves several steps to ensure a snug fit and longevity. Begin by installing tack strips around the perimeter of the room, leaving space for the carpet to tuck in. Lay down carpet padding for comfort and insulation, securing it with staples or adhesive. Roll out the carpet, cut it to fit, and use a power stretcher to stretch it tightly over the tack strips. Trim excess carpet and tuck the edges under the baseboards.
Vinyl Flooring Installation
Vinyl flooring is available in sheets, tiles, or planks and can be installed using different methods, such as glue-down, peel-and-stick, or floating. Ensure the subfloor is smooth and free of imperfections. For glue-down vinyl, apply adhesive evenly and lay the vinyl, pressing it firmly into place. For peel-and-stick tiles or planks, remove the backing and adhere them to the subfloor, ensuring proper alignment and pressing out air bubbles.
Laminate Flooring Installation
Laminate flooring is typically installed as a floating floor, meaning it is not glued or nailed to the subfloor. Start by laying a moisture barrier and underlayment. Begin installing planks along the longest wall, clicking them together using the tongue-and-groove system. Maintain an expansion gap around the perimeter to allow for expansion and contraction. Use spacers to ensure consistent gaps, and trim the last row to fit.
Hardwood Flooring Installation
Hardwood flooring can be installed using several methods, including nail-down, glue-down, and floating. For nail-down installation, nail the planks to the subfloor at an angle through the tongue. For glue-down installation, apply adhesive to the subfloor and press the planks into place. Floating hardwood floors use a tongue-and-groove system similar to laminate flooring. Ensure acclimation of hardwood planks to the room's humidity and temperature before installation.
Tile Flooring Installation
Tile flooring installation involves preparing the subfloor with a cement backer board or similar underlayment. Apply thin-set mortar with a notched trowel and lay the tiles, pressing them firmly into the mortar. Use spacers to maintain consistent grout lines. Once the mortar sets, apply grout to the joints and clean off excess grout. Seal the grout lines to protect them from moisture and staining.
Environmental and Safety Considerations
When installing floor coverings, consider environmental and safety factors. Use low-VOC adhesives and finishes to minimize harmful emissions. Ensure proper ventilation during installation and curing times. Wear appropriate personal protective equipment (PPE), such as gloves, masks, and knee pads, to protect against dust, fumes, and physical strain. Dispose of waste materials according to local regulations to minimize environmental impact.
Cabinetry and Millwork
Cabinetry and Millwork Installation
Cabinetry and millwork must be installed according to the manufacturer's instructions and industry standards to ensure proper function and durability. This includes kitchen and bathroom cabinets, built-in shelving, crown molding, baseboards, and other decorative trim. Proper planning, measurement, and use of appropriate tools and materials are essential for a professional finish.
Cabinet Installation
Begin cabinet installation by marking the layout on the walls and floors, starting with the base cabinets. Secure the base cabinets to the wall studs and ensure they are level and plumb. Install wall cabinets next, using a ledger board to support their weight during installation. Attach the cabinets to the wall studs and each other, ensuring a continuous and level installation. Install trim pieces, doors, and hardware according to the manufacturer’s specifications.
Millwork Installation
Millwork, such as crown molding, baseboards, and door and window casings, should be installed with precision. Measure and cut pieces accurately, using miter joints for corners to ensure a clean fit. Use appropriate adhesives and fasteners, such as finishing nails or brads, to secure millwork in place. Fill nail holes and gaps with wood filler, sand smooth, and apply paint or stain as needed.
Custom Built-Ins
Custom built-ins, such as bookcases, entertainment centers, and closets, require careful planning and design. Measure the space accurately and design the built-in to fit precisely. Assemble components using quality joinery techniques and secure them to the structure of the building. Ensure all shelves and supports are level and capable of bearing the intended loads.
Hardware and Accessories
Install hardware and accessories, such as cabinet pulls, knobs, hinges, and drawer slides, according to the manufacturer's instructions. Ensure that all moving parts operate smoothly and that hardware is securely fastened. Adjust doors and drawers for proper alignment and operation.
Finishing
After installation, complete the finishing touches by caulking gaps between millwork and walls, filling nail holes, and sanding any rough spots. Apply paint, stain, or varnish to match the desired finish and protect the wood. Ensure adequate ventilation when using finishes to allow proper drying and reduce inhalation of fumes.
Environmental and Safety Considerations
When working with cabinetry and millwork, consider environmental and safety factors. Use low-VOC adhesives, paints, and finishes to minimize harmful emissions. Ensure proper ventilation during installation and finishing. Wear appropriate personal protective equipment (PPE), such as safety glasses, gloves, and dust masks, to protect against dust, fumes, and sharp edges. Dispose of waste materials, including sawdust and leftover finishes, according to local regulations to minimize environmental impact.
Drywall
Commonly known as sheetrock, gypsum board, wallboard, plasterboard, or LAGYP, Drywall is the material of choice for constructing most walls and ceilings in buildings. Its installation process is straightforward, and it can be repaired easily. A finished drywall offers a flat, smooth, and uniform surface. It's made from a rock powder that's been compressed and encased in paper.
Before the installation of gypsum wallboard, it's crucial to ensure that the building's exterior is adequately weather-protected and has passed a rough inspection.
The gypsum wallboard should ideally be applied to the ceilings first, followed by the walls. The sheets should be set in place without forcing them together, maintaining a spacing that doesn't exceed 1/4 inch. Whenever possible, tapered edges should be placed adjacent to each other. Precise cutouts, with a maximum allowance of 1/8 inch, should be made for electrical outlets, pipes, and other small fixtures. If any gaps larger than 1/4 inch are present, they must be filled with joint compound and drywall tape. Please refer to the below table for more details.
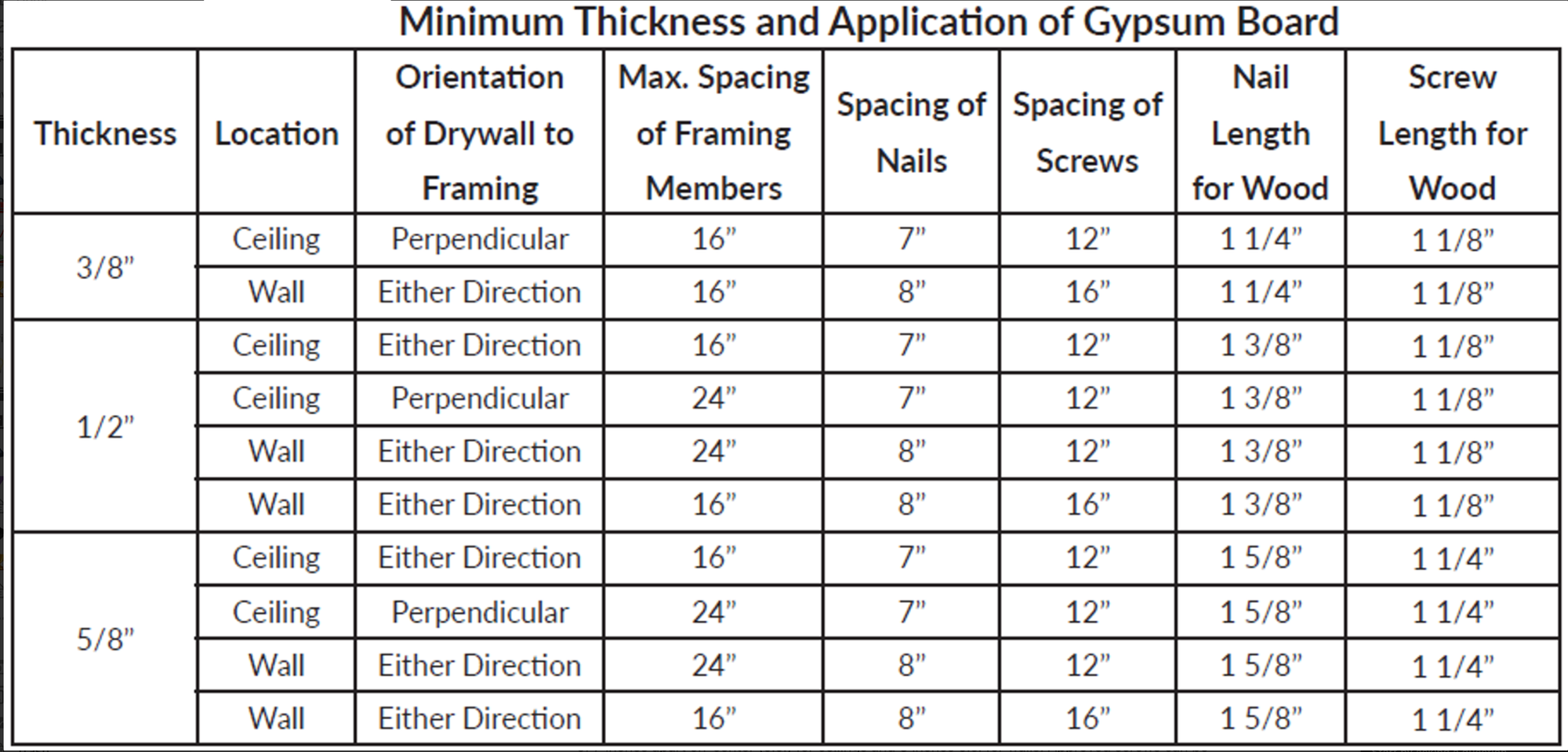
Nailing Drywall
When driving nails into drywall, ensure the head forms a small dimple due to the last hammer strike without fracturing the wallboard. If overdriving causes fractures, they must be rectified by adding more nails. Nails should be positioned 3/8 inch from the edge of the wallboard, with horizontal alignment for nails on adjacent wallboards. The nailing system recommends a spacing of 7 inches apart on-center (o.c.) for ceilings and 8 inches o.c. for walls. Approved screws can be used as an alternative for attaching wallboard, positioned 3/8 inch from the wallboard edges and spaced 12 inches o.c. For pocket doors, screws are required for securing wallboards. Refer to the below image for more details.
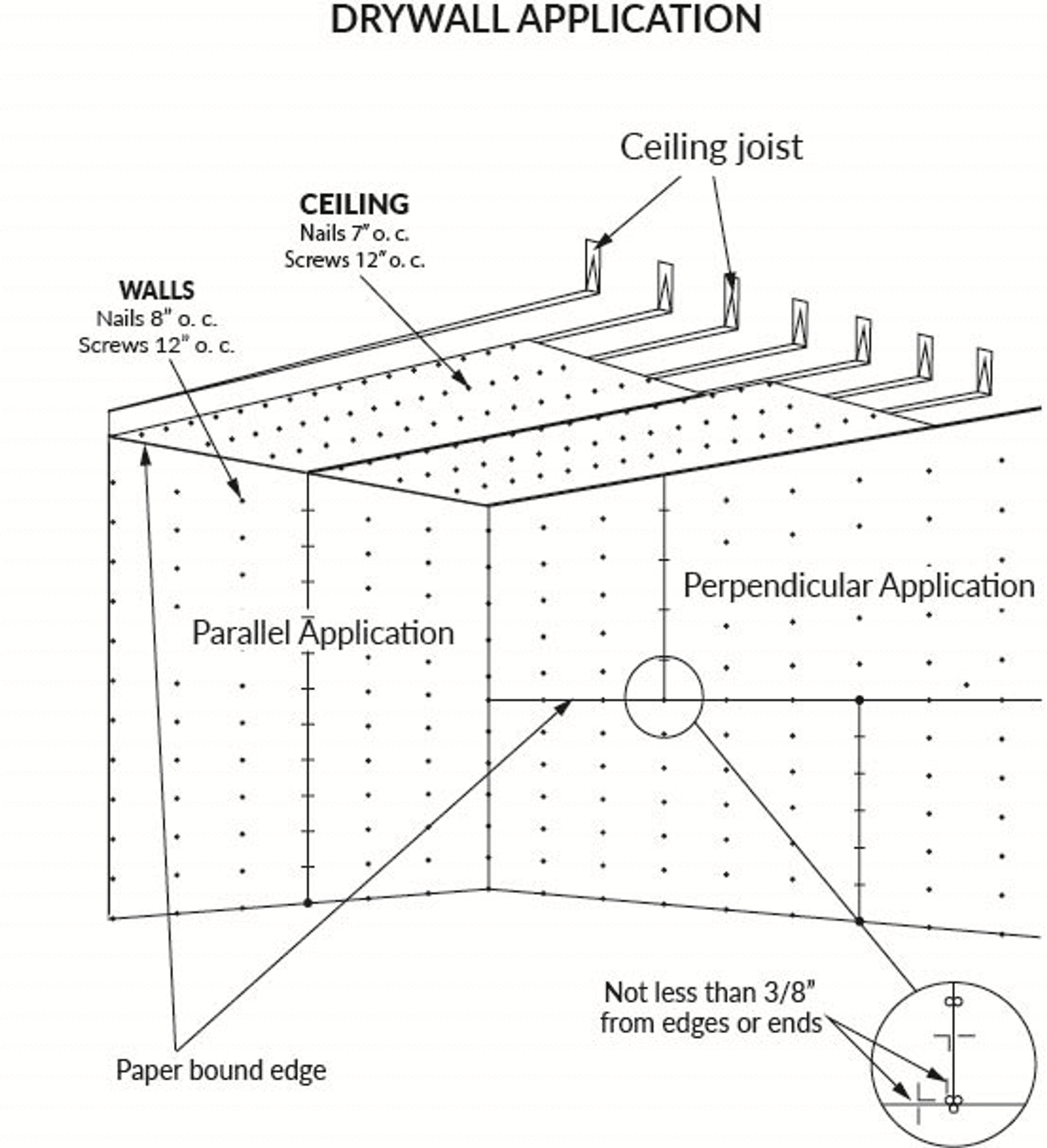
Recommended Fasteners for Drywall
The below tables provide guidelines for the appropriate lengths and spacings of fasteners when attaching gypsum drywall to wood framing.
Gypsum SizeNailsScrews1/2”1 3/8”1 1/8”5/8”1 1/2”1 1/4”CeilingWallsNails 7”Screws 12”Nails 8”Screws 12”
Corners
Corners should be reinforced in such a way that they fit tightly against the wallboard. The recommended nailing distance is approximately 12 inches apart on-center. For “L” edge metal trim, the nails should be spaced every 6 inches. If using paperback corner beading, make sure it is installed following the manufacturer’s guidelines.
Drywall in Shower Enclosures
In environments where high humidity or direct water exposure is likely, such as saunas, showers, or bathtubs, greenboard is not recommended. Instead, the use of cement, fiber-cement, or glass mat gypsum backers is suggested for wall tile bases in these areas.
Drywall in Fire Resistive Construction
In residential buildings, there are specific areas where fire resistive construction, resistant for one hour, is necessary. These areas include the wall that separates an attached garage from the living quarters, and the enclosed spaces under stairways, both walls and ceilings. A standard one-hour firewall can be achieved by nailing 5/8 inch type “X” gypsum wallboard 7 inches on-center to studs spaced 16 inches on-center along all edges. Any gaps and penetrations should be sealed with fire-caulking or tape.
Windows
Window Installation
Windows should be installed following the manufacturer's instructions, and new flashing should be included. Bedroom windows need to comply with certain emergency exit window prerequisites:
- The opening must be at least 5.7 sq ft or 5 sq ft if it's at the same level as the floor.
- The width must be at least 20 inches when fully opened.
- The height must be at least 24 inches when fully opened.
- The bottom of the window opening must not exceed 44 inches from the floor.
These requirements are elaborated in the Emergency Exit Windows section.
Double Pane Windows
Double pane windows, also known as dual pane windows, are the current norm in new residential builds. These double-pane windows are mandatory for windows less than 18 inches from the floor or next to doors. Tempered glass is commonly used in windows less than 18” from the floor. Single pane windows can be used in situations not described above.
Window Sizes in Habitable Rooms
All habitable rooms must have a window or glazed area equivalent to at least 8% of the room's total floor area. The window should be able to open to provide ventilation equivalent to at least 4% of the floor area. For instance, a 100 sq ft room should have a window of minimum 8 sq ft area and a minimum ventilation opening of 4 sq ft.
Bathrooms and water closets need a minimum window opening of 3 sq ft, half of which can be opened. If artificial light or a mechanical ventilation system is available, a glazed area is not necessary.
Emergency Exit Windows
In a residential building, it is mandatory to have one or more operational windows or doors that lead outside in the basement and any bedroom up to the third floor. These are known as emergency exit windows or doors. They need to be functional without the use of any special tools. Even if a room has an exit window or door, it can still have additional smaller windows, which would not serve as exit points.
Minimum Emergency Exit Window Size
Rescue or escape windows need to have a minimum net clear openable area of 5.7 sq ft as shown in the image below The minimum net clear openable height and width of these windows should be 24 inches and 20 inches respectively. If windows are used as escape or rescue routes, their finished sill height should not exceed 44 inches from the floor. This measurement is obtained from the floor to the clear opening of the window, not to the lower edge of the window sill. For windows on the grade-floor, the minimum net clear opening can be 5 sq ft. To determine the required open area, refer to the given formula (in inches) or see the below table:
Minimum emergency Exit Size Guide
!https://contractorsischool.s3-us-west-1.amazonaws.com/ck_files/shares/reading/b/b-figure52.png
!https://contractorsischool.s3-us-west-1.amazonaws.com/ck_files/shares/reading/b/b-table21.png
Skylights
Skylight Installation
Skylights should be installed according to the manufacturer's instructions and industry standards to ensure proper function and durability. Proper planning, measurement, and use of appropriate tools and materials are essential for a professional finish. Skylights can significantly improve natural lighting and ventilation but require careful installation to avoid leaks and structural issues.
Site Assessment and Planning
Before installation, assess the site to determine the best location for the skylight. Consider factors such as roof slope, structural support, and potential obstructions (e.g., rafters, vents, or pipes). Ensure the location allows for adequate daylight while maintaining structural integrity. Obtain any necessary permits and adhere to local building codes.
Roof Preparation
Prepare the roof by marking the skylight's position and cutting the roof opening. Use appropriate safety measures, such as harnesses and guardrails, when working on the roof. Remove roofing materials around the opening and ensure the cut is clean and accurate. Reinforce the opening with headers if necessary to maintain structural support.
Flashing and Waterproofing
Proper flashing and waterproofing are critical to prevent leaks. Install flashing around the skylight according to the manufacturer’s instructions, ensuring a watertight seal. Use roofing cement or sealant where required. Install underlayment or an ice and water shield around the opening to provide additional protection against water infiltration.
Skylight Installation
Place the skylight into the prepared opening and secure it to the roof with screws or nails, following the manufacturer's specifications. Ensure the skylight is level and plumb. Install any additional components, such as curb frames or skylight wells, to direct light and provide insulation.
Interior Finish
Finish the interior around the skylight by installing drywall or other suitable materials. Seal joints and edges with caulk or appropriate sealant to ensure airtightness. Paint or finish the interior to match the surrounding ceiling or wall surfaces.
Ventilation and Condensation Management
For vented skylights, ensure proper operation of ventilation mechanisms. Consider installing blinds or shades to control light and heat. Address potential condensation issues by ensuring proper insulation and ventilation around the skylight. Use double-glazed or low-E glass to improve energy efficiency and reduce condensation.
Maintenance and Safety
Regular maintenance of skylights is important to ensure their longevity and performance. Clean the glass periodically and check for any signs of leaks or damage. Ensure flashing and seals remain intact and functional. For safety, avoid walking on skylights and use proper fall protection when performing maintenance.
Environmental and Safety Considerations
Consider environmental and safety factors when installing skylights. Use energy-efficient skylights to minimize heat loss and gain. Ensure proper insulation and ventilation to improve energy efficiency. Wear appropriate personal protective equipment (PPE), such as gloves, safety glasses, and harnesses, to protect against falls and injuries. Dispose of any waste materials according to local regulations to minimize environmental impact.
Doors
Door Installation
Door installation should adhere to the manufacturer's instructions, industry standards, and California building regulations to ensure proper function, security, and energy efficiency. This includes exterior, interior, and specialty doors such as fire-rated and sliding glass doors.
California Regulations and Requirements
- Egress Requirements: Exterior doors must comply with California Building Code (CBC) egress requirements. Each dwelling unit must have at least one egress door that is operable from the inside without the use of a key, special knowledge, or effort.
- Energy Efficiency: Doors must meet California Title 24 energy efficiency standards. This includes requirements for U-factor and Solar Heat Gain Coefficient (SHGC) for exterior doors to reduce energy consumption.
- Fire Ratings: Fire-rated doors must be installed between the garage and the living space or in other designated fire separation areas. Fire-rated doors must meet the specific rating indicated by the CBC, such as a 20-minute fire rating.
- Accessibility: Doors must meet accessibility standards as outlined in the California Building Code Chapter 11B, ensuring that they are accessible to individuals with disabilities. This includes minimum width requirements and proper hardware for easy operation.
Surface Preparation
Ensure the door frame and surrounding surfaces are level, plumb, and free from defects. Remove any old frames, trim, and debris. Repair any damage to the surrounding structure and install framing or reinforcement as needed to support the new door.
Door Frame Installation
Begin by installing the door frame. Set the frame in the rough opening and shim it to ensure it is level and plumb. Secure the frame to the wall studs with screws or nails, ensuring it is properly aligned. Check that the frame is square by measuring diagonally from corner to corner.
Hanging the Door
Attach hinges to the door and the frame, ensuring they are properly aligned and spaced. Hang the door on the hinges and check for smooth operation. Adjust the hinges as necessary to ensure the door swings freely without binding. Install the strike plate and ensure the latch engages properly with the door closed.
Weatherproofing and Insulation
For exterior doors, apply weatherstripping around the door frame to prevent drafts and improve energy efficiency. Install a door sweep or threshold at the bottom to seal the gap between the door and the floor. Use foam insulation or caulk to seal any gaps between the door frame and the wall.
Interior Door Installation
For interior doors, follow the same steps for hanging and aligning the door. Ensure that interior doors open and close smoothly and latch securely. Install appropriate trim around the door frame to cover gaps and provide a finished appearance.
Hardware Installation
Install hardware such as doorknobs, handles, locks, and deadbolts according to the manufacturer's instructions. For exterior doors, ensure locks and deadbolts provide adequate security. For interior doors, use appropriate hardware for privacy or passage functions as needed.
Finishing
Complete the installation by painting or staining the door and trim to match the surrounding decor. Sand and smooth any rough areas before applying finishes. Ensure proper ventilation when using paints and stains to allow for drying and reduce inhalation of fumes.
Maintenance and Safety
Regular maintenance of doors is important to ensure their longevity and performance. Check and tighten hardware periodically. Lubricate hinges and locks as needed to ensure smooth operation. For safety, ensure all exterior doors are properly secured and check fire-rated doors for any damage or wear that might compromise their effectiveness.
Environmental and Safety Considerations
Consider environmental and safety factors during door installation. Use low-VOC paints and finishes to minimize harmful emissions. Ensure proper ventilation during installation and finishing. Wear appropriate personal protective equipment (PPE), such as gloves, safety glasses, and dust masks, to protect against dust, fumes, and sharp edges. Dispose of waste materials according to local regulations to minimize environmental impact.
Landscaping
Landscaping Installation
Landscaping should be designed and installed according to local regulations and best practices to ensure aesthetic appeal, functionality, and sustainability. This includes the selection and planting of trees, shrubs, flowers, and ground cover, as well as the installation of irrigation systems, hardscaping elements, and outdoor structures.
California Regulations and Requirements
- Water Efficiency: California's Model Water Efficient Landscape Ordinance (MWELO) sets standards for water-efficient landscaping, including irrigation system design, plant selection, and soil management. Landscapes over a certain size must comply with MWELO to reduce water usage.
- Permits: Certain landscaping projects, such as large retaining walls, outdoor kitchens, and significant grading, may require permits. Check with local building departments for specific requirements.
- Native and Drought-Tolerant Plants: Encourage the use of native and drought-tolerant plants to reduce water usage and support local ecosystems. California has a diverse range of native plants suitable for various climates and soil types.
Site Assessment and Planning
Conduct a thorough site assessment to understand the soil conditions, sunlight exposure, drainage patterns, and existing vegetation. Develop a landscaping plan that considers these factors and addresses the client's needs and preferences. Ensure the plan complies with local regulations and sustainability practices.
Soil Preparation
Prepare the soil by removing weeds, debris, and old plant material. Test the soil pH and nutrient levels, and amend it as necessary with compost, organic matter, or other soil conditioners. Proper soil preparation promotes healthy plant growth and reduces the need for fertilizers and pesticides.
Plant Selection and Installation
Choose plants that are suited to the local climate, soil conditions, and water availability. Group plants with similar water and sunlight requirements together to create hydrozones for efficient irrigation. Dig planting holes twice as wide and just as deep as the root ball to encourage root growth. Water plants thoroughly after planting and apply mulch to retain moisture and suppress weeds.
Irrigation Systems
Design and install irrigation systems that comply with MWELO standards and promote water efficiency. Use drip irrigation or soaker hoses for garden beds and low-volume sprinkler heads for lawns. Install smart controllers that adjust watering schedules based on weather conditions. Regularly check and maintain the system to ensure efficient operation.
Hardscaping Elements
Incorporate hardscaping elements such as patios, walkways, retaining walls, and outdoor kitchens into the landscaping plan. Use permeable materials where possible to reduce runoff and promote groundwater recharge. Ensure that hardscaping features are installed on stable, well-compacted bases to prevent shifting and settling.
Outdoor Structures
Install outdoor structures such as pergolas, arbors, and gazebos to provide shade and create focal points in the landscape. Ensure these structures comply with local building codes and are constructed with durable, weather-resistant materials.
Lighting
Incorporate outdoor lighting to enhance the landscape's beauty and functionality at night. Use energy-efficient LED fixtures and solar-powered lights to reduce energy consumption. Properly plan and install lighting to highlight key features and ensure safety along pathways and entryways.
Maintenance and Sustainability
Regular maintenance is crucial for a healthy, attractive landscape. This includes watering, pruning, fertilizing, pest control, and weeding. Use sustainable practices such as composting yard waste, applying organic fertilizers, and implementing integrated pest management (IPM) to minimize environmental impact.
Environmental and Safety Considerations
Consider environmental and safety factors throughout the landscaping process. Use native and drought-tolerant plants to conserve water and support local wildlife. Implement erosion control measures on slopes to prevent soil loss. Ensure proper handling and disposal of chemicals and waste materials to protect the environment. Wear appropriate personal protective equipment (PPE) when using power tools and handling plants and chemicals. Dispose of waste materials according to local regulations to minimize environmental impact.