Safety
The Safety section, which makes up approximately 12% of the trade Exam, covers essential safety protocols and regulations critical for maintaining a secure work environment on construction sites. This section emphasizes personnel safety, transportation and traffic control, and environmental safety, encompassing the use of scaffolding, electrical safety, personal protective equipment (PPE), ladder safety, excavation protocols, fire prevention, and asbestos handling. It also addresses the importance of OSHA and Cal/OSHA regulations, ensuring that contractors are aware of the legal responsibilities to protect their workers and the public from potential hazards. Understanding and implementing these safety measures are crucial for passing the exam and ensuring that construction projects comply with state safety standards.
Scaffolding
A permit from DOSH is required to erect a scaffold that stands 3 stories (36 feet) or higher. Steel and iron are the most commonly used materials for scaffolding in the United States, although various other materials can also be used. The correct usage of scaffolds can aid in preventing workplace accidents and injuries.
Scaffolds become necessary when employees cannot safely perform their work while standing on permanent or solid construction that is at least 20 inches wide or on ladders.
Exception 1 - Work of short duration that is less than 20 inches in width and does not exceed a fall distance of 15 feet in height, given that adequate risk control is provided.
Exception 2 - Temporary work from joists or similar members at 2 feet or closer centers, where planks resting on these members form a plank platform 12 inches wide or provide equivalent protection.
The employer is responsible for meeting the safety standards of DOSH (Cal/OSHA) regulations. The employer must designate a competent person with the authority to implement corrective measures when these standards are not adhered to. The erection, moving, dismantling, or alteration of a scaffold must only be conducted under the direct supervision of a competent person qualified in these activities. It is also compulsory for a competent person to inspect the scaffold prior to the commencement of each work shift.
Each scaffold must be designed and constructed with a dead load safety factor that ensures the scaffold can support its own weight and 4 times the maximum intended working (live) load applied or transmitted to it without failure. The maximum intended working loads are as follows:
Light-duty scaffolds: 25 pounds per square foot of work platform.
Medium-duty scaffolds: 50 pounds per square foot of work platform.
Heavy-duty scaffolds: 75 pounds per square foot of work platform.
Special-duty scaffolds: those exceeding 75 pounds per square foot of work platform as determined by a qualified person or a Civil Engineer registered with the State of California and experienced in scaffold design.
Here are some general guidelines for the construction of scaffolding:
- Scaffolds must be erected to be plumb, level and square.
- The scaffold manufacturer's railings must be installed on the open sides and ends of work platforms that are 7 1/2 feet or more above grade.
- The end of each platform that is 10 feet or less should not extend more than 12 inches beyond its support.
- Each platform that measures 10 feet in length should not extend over its support by more than 18 inches.
- Supported scaffolds that are more than four times the minimum base width (4:1) must be tied, guyed or braced.
- Planking should be a minimum of 2” thick and 10” inches wide.
- Fall protection systems are required on any scaffold that is more than 10 feet above a lower level.
- Although scaffolds are typically built from the ground up, they should be dismantled from the top down.
There are three fundamental scaffold types: supported scaffolds, suspension scaffolds, and aerial lifts.
Supported scaffolds are structures consisting of one or more platforms held up by rigid supports like outrigger beams, brackets, poles, legs, uprights, posts, or frames.
Suspension scaffolds are platforms hung by ropes or other flexible means from an overhead structure.
Aerial lifts refer to vehicle-mounted devices like cherry pickers or boom trucks, utilized to elevate a worker to a higher position.
There are also several specific types of scaffolding that were not included due to formatting issues:
- Fabricated Frame Scaffold
- Manually Propelled Mobile Scaffold
- Tube and Clamp Scaffold
- System Scaffold
- Ladder Jack Scaffold
- Pole or Wood Pole Scaffold
- Pump Jack Scaffold
- Two Point Suspension Scaffold
- Prohibited Scaffold
Scaffold Safety
Cal/OSHA mandates that employers should provide retraining to employees who might lack the necessary skills or comprehension for secure operation during the assembly, usage, or disassembly of scaffolds. This implies that the employer will continue training the employee until they achieve the required level of expertise to operate safely.
Previously mentioned, the most prevalent hazard encountered by workers on scaffolds is falling. Yet, another risk to consider is electrocution, since regulations specify mandatory clearance distances from overhead power lines. Should scaffolding be situated near an insulated power line of below 300 volts, it must maintain a minimum distance of 3 feet. For non-insulated lines, the minimum distance must be 10 feet.
Electrical Safety
The flow of electrons, which is inherent to all electrical devices, presents a potential risk of electrocution. This risk is amplified in a workplace setting where temporary power sources, power tools, lighting, fans, pumps, among other equipment, are in use.
There are four primary categories of electrical injuries that may occur in the workplace: electrocution, electrical shock, burns, and indirect injuries.
- Electrocution: This refers to a severe electrical shock, where the victim experiences serious symptoms. These may include burns, nerve damage, muscle contractions, cardiac arrest, and paralysis, among others. Electrocution can cause both internal and external damage and often results in death.
- Electrical Shock: This occurs when a body completes an electrical circuit. This can happen when the body connects with both wires of an electrical circuit, or one wire of an energized circuit and the ground. The severity of the shock is dependent on the amount and frequency of the current, the current's path, and the duration of exposure.
- Burns: This is the most frequent type of injury related to electrical shocks, and it has three major types:
- Electrical burns, which are caused by the heat generated as electrical current passes through the body.
- Arc or Flash burns, which are caused by electrical arcs or explosions of high intensity.
- Thermal contact burns, which occur when skin comes into contact with overheated electrical equipment or when clothing catches fire from sparks.
- Indirect Injuries: These are injuries that occur as a result of an electrical shock that either triggers a surprise reaction, causing the victim to fall, or causes a loss of muscle function leading to a fall.
Current Level (Milliamperes): 1 mA
- Likely Impact on Human Body: Perception level. Minor tingling feeling. Potentially dangerous under certain circumstances.
Current Level (Milliamperes): 5 mA
- Likely Impact on Human Body: Minor shock experienced; not painful but unsettling. The average person can let go. However, involuntary reactions to shocks in this range may result in injuries.
Current Level (Milliamperes): 6 mA - 16 mA
- Likely Impact on Human Body: Painful shock, onset of loss of muscular control. Often referred to as the "let-go" range or freezing current.
Current Level (Milliamperes): 17 mA - 99 mA
- Likely Impact on Human Body: Extreme pain, respiratory failure, severe muscle contractions. The individual is unable to let go. Death is a possibility.
Current Level (Milliamperes): 100 mA - 2,000 mA
- Likely Impact on Human Body: Ventricular fibrillation (irregular, uncoordinated contraction of the cardiac muscle). Commencement of muscle contraction and nerve damage. Death is probable.
Current Level (Milliamperes): Greater than 2,000 mA
- Likely Impact on Human Body: Cardiac arrest, damage to internal organs, and severe burn injuries. Death is highly likely.
Preventing electrical hazards involves identifying and managing existing hazards. Actions such as finding exposed electrical components, repairing damaged equipment, avoiding circuit overloads, grounding electrical devices properly, and ensuring adequate wiring are examples of preventative steps. For instance, turning off a circuit before commencing work on it can significantly reduce electrical hazards.
Electrical hazards can often be identified through unusual occurrences or behavior. If, for instance, circuit breakers or ground fault circuit interrupters frequently trip, it's highly likely that an electrical hazard exists and it should be promptly addressed. Other indicators might include the smell of burning, unusually hot wiring, damaged insulation or an abnormal reading from a tester. Two common strategies for safeguarding oneself from these dangers involve the use of insulation on wiring and grounding of circuits.
- Insulation involves wrapping nonconductive material such as plastic around the conductor. This aids in reducing or completely stopping the flow of current. Conductors used in equipment grounding are often insulated with wires that are either green or green with yellow stripes.
- Grounding refers to the process of creating a direct connection to a known ground. This action can prevent the undesirable accumulation of voltages that could potentially cause an accident. Conductors that are grounded usually have a white color.
According to Cal/OSHA, two types of grounding are required:
- Service ground is a grounded wire that is either white or grey in color. This wire is grounded both at the generator and at the service entrance of the building. It plays an important role in protecting machines, tools, and insulation.
- Equipment ground offers an alternative path from the equipment to the ground. This kind of ground provides additional protection for workers, especially if a malfunction leads to the metal parts of a device becoming energized.
In order to ensure that equipment grounding is properly executed, OSHA requires two tests to be conducted by a competent individual. The first test, a continuity test, verifies that the equipment grounding conductor is electrically continuous. This test should be conducted on all cords, receptacles that aren't part of permanent wiring, and equipment that is grounded and connected by a plug. The second test, performed on receptacles and plugs, ensures that the equipment-grounding conductor is connected to the correct terminal. These tests can be carried out using various tools, including a continuity tester, a lamp and battery, a bell and battery, an ohmmeter, or a receptacle tester. After any repairs, these tests should be conducted at intervals of 3 and 6 months.
Ground-Fault Circuit Interrupter (GFCI)
The use of a Ground Fault Circuit Interrupter (GFCI) can be an effective measure to prevent electrical hazards. GFCIs can detect ground faults and promptly interrupt power in the circuit. They can also sense discrepancies in the amount of current entering and leaving a device; if a deviation as small as 5mA is detected, a GFCI will disconnect power in 1/40th of a second. GFCIs are typically utilized in damp environments such as bathrooms and kitchens. Employers are mandated to supply approved GFCIs for all 120-volt, single phase, 15 to 20 ampere receptacle outlets not part of the building's permanent wiring.
Regulations from the NEC and OSHA specify that specific types of flexible cords must be used in construction environments. These cords should connect to devices and fittings in a way that prevents stress at joints and terminal screws. On construction sites, flexible cords can be damaged by sharp objects, exposing electrical conductors. Acceptable uses for flexible cords include elevator cables, wiring for cranes and hoists, noise prevention, and appliances designed for easy removal for maintenance or repair. Flexible cords should not be used where frequent inspections are not feasible. They should not be routed through walls, ceilings, doorways, windows, or concealed areas such as conduits or other raceways.
Improper use of electrical equipment can pose significant risks to the user, and OSHA may levy a monetary penalty for such misuse. Regular inspection of electrical equipment is crucial for safety, as a defective cord or wire can inflict serious harm on the user. If a cord or wire is damaged or exposed, the power tool or cord must be labeled “Do Not Use” and promptly replaced.
When using power tools, adhere to these basic guidelines:
- Disconnect power when not in use, or before servicing or changing blades or attachments.
- Position cords and hoses away from heat, oil, and sharp edges.
- Never transport tools by the cord or hose.
- Refrain from pulling cords from plugs or sockets.
- Maintain a safe distance from others not involved in the operation.
- Avoid usage in wet or damp locations.
- Operate within the limitations of the design.
- Use appropriate gloves and footwear.
The most effective way to prevent or avoid electrical hazards is to apply common sense. A basic understanding of Cal/OSHA’s regulations and a touch of common sense could potentially save a life.
Personal Protective Equipment
Personal Protective Equipment, often abbreviated as PPE, must adhere to or surpass the standards set by the American National Standards Institute (ANSI). While employees can bring their own PPE to the workplace, it needs to align with or exceed ANSI's requirements and obtain employer approval.
It's crucial to remember that PPE serves as the final protective measure after implementing engineering controls, safe work practices, and administrative measures.
- Engineering controls refer to the physical modification of a machine or the workplace environment to mitigate occupational hazards.
- Work practices entail training employees to lessen their exposure to workplace hazards.
- Administrative controls focus on the manner and timing of workers' job performance, such as scheduling practices and worker rotation aimed at reducing hazard exposure.
Since November 15, 2007, employers are obligated to furnish appropriate PPE to employees at no cost. Employers continue to strive to identify and manage workplace hazards. They also provide training to employees on the correct use and maintenance of PPE. Such training should encompass the necessity of specific PPE types, their protective attributes, limitations, wear and maintenance timelines, how to spot signs of wear and tear, cleaning methods, and their expected lifespan. Employers are required to maintain records of all PPE training, providing certificates that list the trained employees, the training dates, and the specific training subjects.
Head Protection
Hard hats, designed to withstand object penetration and absorb impact, should be water-resistant and slow-burning. Their design should come with clear instructions for adjusting the suspension and headband. Hard hats come in three classes:
- Class A hard hats offer resistance to impacts and penetration, alongside restricted voltage protection (up to 2,200 volts).
- Class B hard hats deliver the utmost protection against electrical hazards, offering shock and burn protection against high-voltage (up to 20,000 volts). In addition, they protect against hazards caused by flying or falling objects.
- Class C hard hats offer protection that is lightweight and comfortable, although they do not provide any protection against electrical hazards.
Eye and Face Protection
Defending against threats to the eyes and face can involve utilizing equipment such as glasses, goggles, face protectors, specialized helmets, and shields for welding.
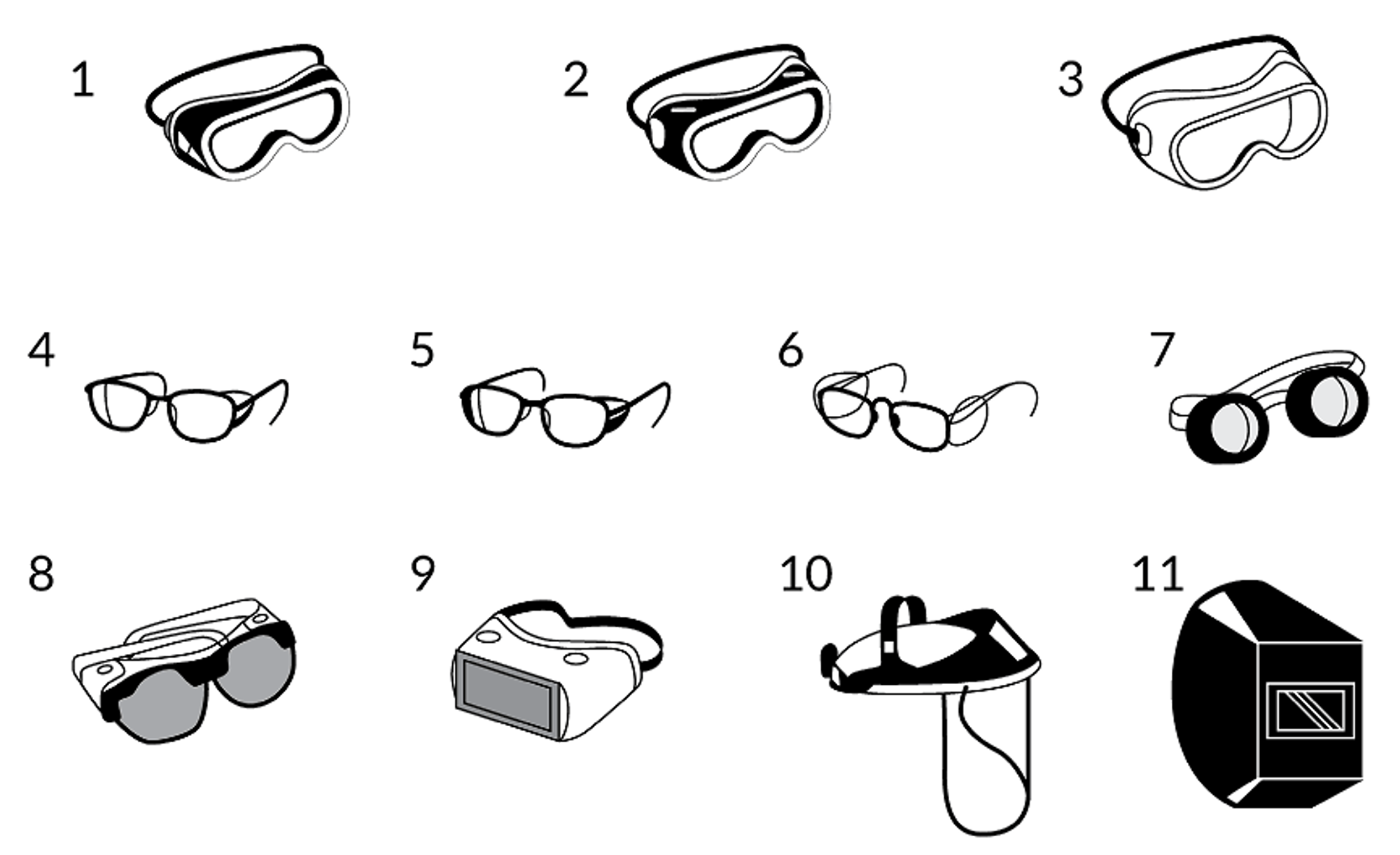
- Goggles, flexible fitting with regular ventilation
- Goggles, flexible fitting with hooded ventilation
- Goggles, cushioned fitting with a rigid body
- Spectacles, metal frame with side shields
- Spectacles, plastic frame with side shields
- Spectacles, metal-plastic frame with flat-fold side shields
- Welding goggles, eyecup type with tinted lenses
- Welding goggles, eyecup type with tinted-plate lense
- Welding goggles, coverspec type with tinted-plate lense
- Face shield can be plastic or mesh either tinted or clear
- Welding helmet
Hearing Protection
Sound levels are gauged in decibels on the A-Scale (dBA). According to Cal/OSHA’s regulations, hearing personal protective equipment (PPE) becomes a necessity when an employee is subjected to a noise level exceeding an 8-hour time-weighted average of 90 dBA (a 100 percent dose). This implies that if an employee's exposure to 90 dBA persists throughout an 8-hour workday, they must utilize earplugs or earmuffs.
All employees who experience an 8-hour TWA of 85 dBA or higher must be included in a Hearing Conservation Program (HCP). This program has five key components:
- Monitoring of exposure
- Audiometric testinga) The results of these tests must be retained for the duration of the employee’s employment.
- Provision of hearing protection
- Training for employeesa) Training must be provided annually
- Recordkeeping (Records of noise exposure must be kept for a period of 2 years)
The most common forms of hearing protection are single-use earplugs, molded (pre-formed) earplugs, and earmuffs. Single-use earplugs are typically made from waxed cotton, foam, silicon rubber, or fiberglass wool. After insertion, these earplugs adapt to the shape of your ear, providing adequate protection. Molded or pre-formed earplugs are the second type, which are professionally fitted. These earplugs can either be reusable or disposable and should be cleaned after each use. Earmuffs provide coverage for the entire ear, creating a perfect seal; therefore, any eyewear that disrupts this seal can diminish the effectiveness of the earmuffs.
Hand and Arm Protection
There exists a variety of gloves, each designed to protect from different hazards. Some gloves are designed to shield from abrasions, others from chemical or thermal burns, and others from cuts, bruises, and punctures. Employers are tasked with training their workforce to select the appropriate hand PPE for their specific tasks. It's important to note that asbestos gloves and asbestos linings are disallowed. Below is an OSHA-approved list of different glove types:
- Leather gloves serve as a shield against sparks, moderate heat, blows, chips, and other coarse objects.
- Aluminized gloves offer reflective and insulative protection from heat or cold. Their inserts consist of synthetic materials that help safeguard the wearer from temperature extremes. They are ideal for welding tasks.
- Gloves made from Aramid fiber offer resistance to heat and cold and have a good lifespan. These gloves can also resist cuts and abrasion.
- Gloves manufactured from other synthetic materials offer protection against heat and cold. They also provide resistance to cuts and abrasion. These synthetic gloves aren't suitable for alkalis and solvents.
Fabric and coated fabric gloves offer protection against dirt, splinters, chafing, and abrasions. They're not suitable for handling rough, sharp, or heavy materials. Coated fabric gloves are general-purpose gloves offering slip-resistance. These gloves can be used when handling bricks or ropes.
Gloves that are chemical and liquid resistant are also available. They're made from plastic or rubber materials. OSHA provides a list of four types of chemical-resistant gloves:
Butyl gloves, made of synthetic rubber, offer protection against acids, peroxides, oxidations, and corrosions.
Natural (latex) rubber gloves are considered general-purpose gloves and provide good protection against acids, alkalis, salts, and ketones.
Neoprene gloves, made of synthetic rubber, offer good flexibility, finger dexterity, high density, and tear resistance.
Nitrile gloves, made from a type of plastic called copolymer, can protect against solvents.
Body Protection
Employees encountering hazards such as extreme heat or cold, splashes from molten materials or hot fluids, impacts from tools or machinery, and harmful chemicals must utilize suitable body protection. Examples of body PPE range from lab coats and vests to aprons, coveralls, surgical gowns, and full-body suits.
Body protection encompasses various materials, each tailored to shield against a specific type of threat. Here are five material types outlined by OSHA:
- Paper-like fiber is utilized for disposable suits that guard against dust and splashes of various types.
- Treated wool and cotton are adapted for temperature fluctuations, offer fire resistance, comfort, and safeguard against dust, abrasions, and irritants.
- Duck, a densely woven cotton fabric, is good for protection against cuts and bruises.
- Leather is ideal for defending against dry heat and flames.
- Rubberized fabrics, neoprene, and plastics are best suited for protection against chemicals and certain acids.
Foot and Leg Protection
Engaging in worksite activities means you could potentially step on sharp objects, slide on slick surfaces, experience an electric shock from a live wire, get splattered with molten metal, or have a heavy item drop on your feet. Essentially, if you're exposed to any of these hazards, it's mandatory to wear appropriate footwear that is both impact and heat resistant.
In cases of electrical hazards, safety-toe shoes should be nonconductive, preventing the wearer from forming an electrical circuit to the ground. The shoes must be capable of safeguarding against up to 600 volts in dry conditions and should be incorporated with other preventative strategies to lessen electrical hazards. Just like all other PPE, it's crucial to understand how to properly care for and maintain foot protection. The employee must be aware when the protective gear is no longer effective or fails to provide the necessary protection. Once the equipment is compromised and loses its protective qualities, it needs to be immediately replaced.
Excavations, Trenching and Shoring
Before initiating an excavation or digging project at a worksite, it is mandatory to notify the Underground Service Alert. This service, operating free of charge across California, performs damage prevention functions. They assess all excavation plans, dispatch a team to pinpoint areas close to the proposed excavation or digging project, and mark the underground utilities ingress into the property.
The Underground Service Alert must be contacted a minimum of 2 days and a maximum of 14 days before the excavation work begins.
- Negligent failure to inform the Underground Service Alert can result in fines up to $10,000.
- Intentional non-compliance can attract penalties up to $50,000.
The marking of the grounds will be performed using a color-coded system of abbreviated stakes and markings, each color indicating a different type of facility.
- White: Proposed Excavation
- Red: Electric Power Lines, Cables, Conduit, and Lighting Cables
- Orange: Communication, Alarm, or Signal Lines, Cables, or Conduit
- Purple: Reclaimed Water, Irrigation, and Slurry Lines
- Pink: Temporary Survey Markings
- Yellow: Gas, Oil, Steam, Petroleum, or Gaseous Materials
- Blue: Potable Water
- Green: Sewers and Drain Lines
When it comes to trench excavation, keep in mind the following numerical guidelines that correspond to state requirements:
- 2 Feet: Required distance for spoils piles from edge of excavation/trench
- 3 Feet: Length the ladder must extend above excavation/trench
- 4 Feet: Depth at which a ladder or ramp is required for access and exit
- 5 Feet: Depth at which mandatory shoring, benching, and/or a protection system is required
- 6 Feet: Depth at which fall protection is required for bridges/walkways across excavations/trenches
- 20 Feet: Shoring designed by a registered engineer is required
- 25 Feet: Maximum travel distance to an exit ladder
Sloping
The term "maximum allowable slope" refers to the steepest vertical-to-horizontal ratio that an excavation wall can have to maintain stability. It's a method of reducing excavation instability by angling the soil.
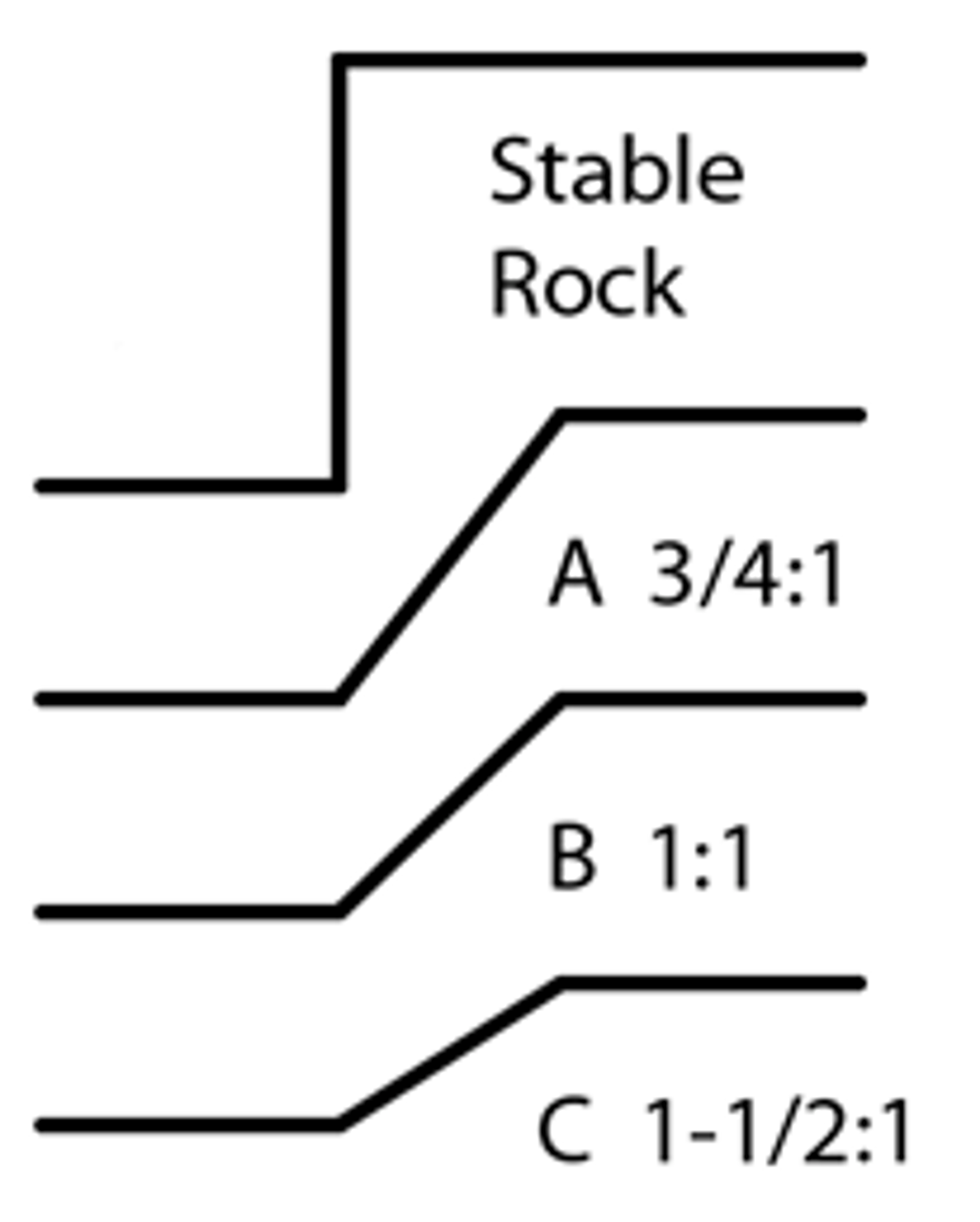
Type A soil stipulates that for every single foot of trench depth (V), the excavation must extend ¾ of a foot backward (H).
Type B soil dictates that for each foot of trench depth (V), the excavation must retreat by 1 foot (H).
Type C soil necessitates a 1-1/2 foot retreat (H) for each foot of trench depth (V).
All basic slope excavations with a depth of 20 feet or less should have a maximum allowable slope of 1-1/2:1. This gradient or less is safe for any soil type. If the excavation is entirely in stable rock or is less than 5 feet in depth, and a competent person has inspected the ground and found no potential for a cave-in, protective systems are not necessary.
Shoring
Shoring, in the context of trenches, involves the employment of various methodologies such as metal-hydraulic, mechanical or timber shoring to stabilize trench walls and prevent collapses. Cal/OSHA's regulations dictate that all trenches exceeding 5 feet in depth must have an approved shoring system in place prior to the commencement of work.
The installation of hydraulic shoring sections necessitates a minimum of two pump cylinders. Should sheeting be affixed to the jacks, utilizing a hoe would be the most effective method of inserting the shoring system into the trench. The jacks should be evenly distributed to ensure the provision of ample workspace for workers.
Implementing hydraulic shoring systems involves these key steps:
- Position the shoring system, which should be collapsed or folded, adjacent to the trench
- Adjust the jack so that the hydraulic quick coupler faces upwards
- Connect the pump hose to the quick coupler after unfolding the shore
- Activate the hydraulic cylinders
- Insert the shore into the trench and secure it into the sheathing
- For shoring systems removal, drain the fluid from the hydraulics
In certain scenarios, shoring systems may not provide sufficient protection due to the excessive depth of the trenches. Consequently, a shield may be required. Also referred to as trench boxes, trench shields are employed in such circumstances.
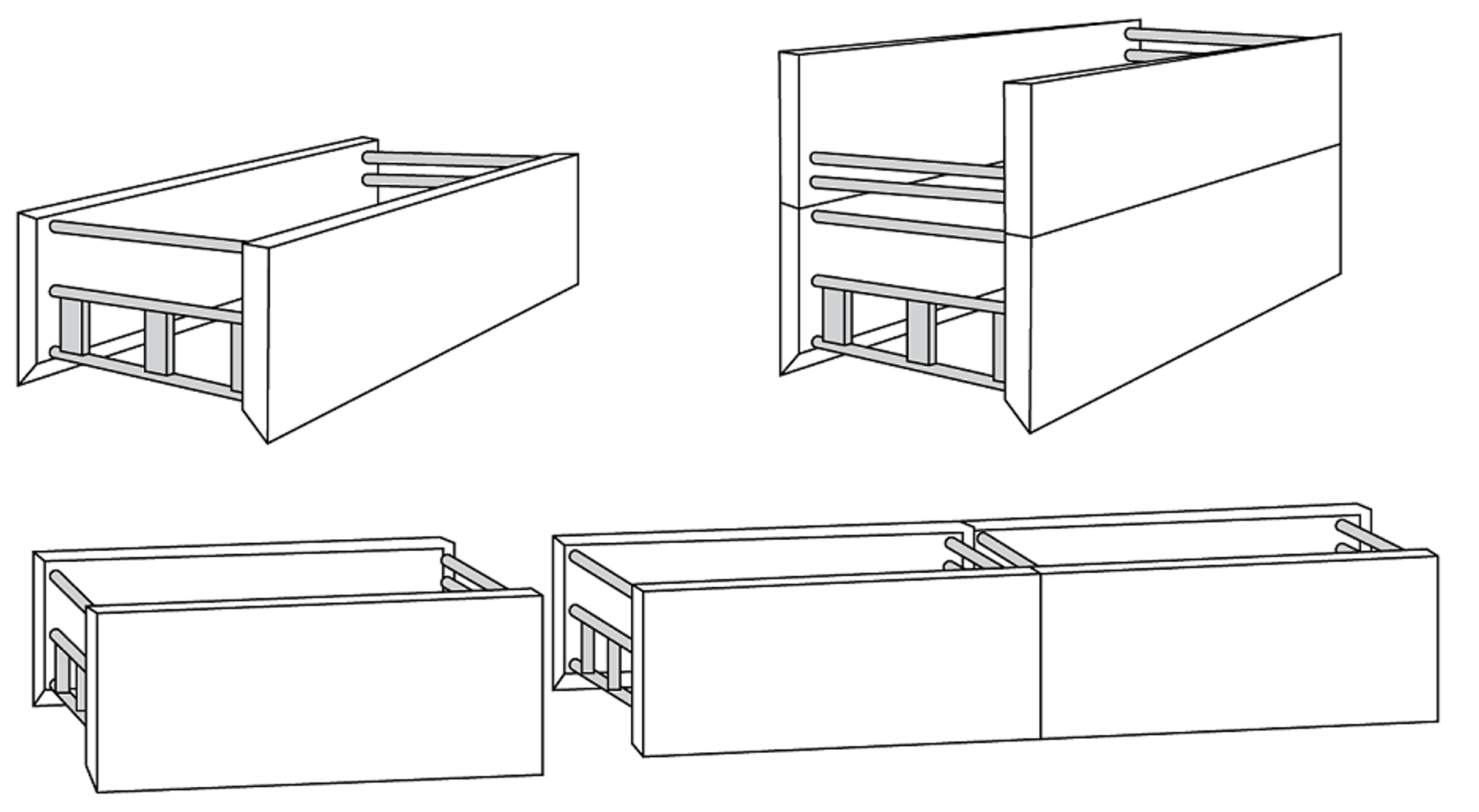
The following are the requirements for a shield system:
- The design of the shield system should be such that it can handle the loads it is subjected to without failure.
- Shields should be positioned in a way that prevents sudden, hazardous lateral movements. Safe entry and exit from areas protected by shields should be ensured for employees.
- While shields are being installed, removed, or moved vertically, employees should not be inside them.
- For compound excavations, shield sides should extend at least 18 inches above the vertical walls. For vertically cut trenches, the shield should reach at least to the trench's catch point. Excavating earth material up to 2 feet below the bottom of a shield is permitted, provided the shield is designed to withstand the forces calculated for the full trench depth, and there are no signs of potential soil loss from behind or below the shield bottom while the trench is open.
Records and Reporting
Form 300
California obliges employers to maintain a record of work-related illnesses and injuries using Form 300. This record should include each work-related fatality and any work-related injury or illness that results in unconsciousness, restricted work activity or job transfer, days off work, or medical treatment beyond first aid. It should also detail any significant work-related injury or illness diagnosed by a licensed healthcare professional or physician. For each injury or illness recorded, an Injury and Illness Incident Report (Cal/OSHA Form 301) or an equivalent form must be completed. In case there's uncertainty about a case recordability, employers can seek guidance from their local Cal/OSHA office.
In situations where an employer has more than 10 employees, the year-end totals from log 300 should be transferred to log 300A, which must be displayed from February 1 to April 30 each year. Employers must also provide reasonable access to the Log and Summary of Occupational Injuries and Illnesses, Cal/OSHA form 300, to employees, former employees, and their representatives. In addition, employee medical records and exposure records must be accessible to employees or their authorized representatives.
Form 5020
When a severe injury, illness, or death occurs, it must be reported to Cal/OSHA within 8 hours. Subsequently, Form 5020 must be completed, which serves as the official report for a severe injury, illness, or death. In this scenario, employers are obliged to submit Form 5020 within 5 days after becoming aware of the serious injury, illness or death.
Employers must promptly provide the name and address of their workers’ compensation insurance provider to the physician to facilitate the timely submission of the doctor’s first report. For self-insured employers, the report must be directly filed with the Division of Labor Statistics and Research within five days after the employer learns about the injury, illness or death. Moreover, the self-insured employer must send the doctor’s report (Form 5021) to the Division of Labor Statistics and Research within 5 days of receipt.
Reporting Severe or Fatal Accidents
It is mandatory for employers to promptly notify the nearest Cal/OSHA district office of any incidents relating to severe injuries, illnesses, or fatalities that are suspected to be work-related. This notification must be made via phone or fax and should occur within 8 hours of the incident. Information to be conveyed includes the injured person's name and employer, a description of the accident, its nature, and location, the date and time it occurred, the identity of the person reporting the incident, the treatment location of the injured, and a list of other agencies that responded to the incident.
Understanding OSHA
OSHA (Occupational Safety & Health Act)
The Occupational Safety & Health Act, also known as OSHA, was enacted by Congress and signed into law by President Nixon in 1970. Its primary function is to assist employers and employees in minimizing job-related injuries, illnesses, and deaths. Since its establishment, OSHA has contributed to a 60% reduction in job-related deaths and a 40% reduction in on-the-job injuries.
OSHA's objectives include:
- Enforcing safety regulations
- Facilitating employers and employees in training regarding regulations & guidelines
- Collaborating with voluntary programs dedicated to workplace safety
Also recognized as Public Law 91-596, OSHA applies to most private sector employers and employees. However, it does not cover self-employed individuals or federal agencies, which have their own sets of worker safety and health guidelines. Religious groups come under OSHA's ambit if they employ workers for non-religious purposes, such as gardening or maintenance.
OSHA is a federal entity and acts as the chief regulatory and enforcement authority for workplace health and safety in the United States. Nevertheless, 26 states and jurisdictions, including California, have elected to establish their own job safety and health programs. These state-level programs are subject to OSHA's approval and monitoring. Essentially, these state-level programs can enforce stricter standards and regulations than those stipulated by federal OSHA. Conversely, if federal OSHA sets a more stringent standard or a regulation for a hazard not covered by a state, the state has six months to align its state-level program with the federal rules.
Cal/OSHA: A State-Level OSHA Program in CaliforniaIn 1973, California introduced its own OSHA program known as Cal/OSHA. This program mandates strict adherence to standards outlined in Title 8 of the California Code of Regulations. Cal/OSHA diverges from federal standards in several key areas. It necessitates an illness prevention program and has more rigorous criteria for hazardous communications and chemical exposure limits. In instances where federal standards are lacking, state-level standards must be followed. The Division of Occupational Safety and Health (DOSH) is responsible for enforcing Cal/OSHA standards.
Duties of California Employers Under Cal/OSHACalifornia employers are bound by numerous responsibilities under the California Occupational Safety and Health Act of 1973 and Title 8 of the California Code of Regulations. These responsibilities include:
- The development, execution, and maintenance of an Injury and Illness Prevention Program.
- Inspection of workplaces to identify and rectify unsafe conditions.
- Ensuring employees are equipped with, and use, safe tools and equipment.
- The use of signs, labels, posters, or color codes to alert employees to potential hazards.
- Provision of necessary medical examinations and training as per Cal/OSHA standards.
- Immediate reporting of any employee's serious injury, illness, or death to the nearest Cal/OSHA Enforcement Unit district office via telephone or fax.
- Displaying the Cal/OSHA poster in a visible location to inform employees of their rights and responsibilities.
- Providing the names of authorized employee representatives who may accompany enforcement personnel during inspections to Cal/OSHA enforcement personnel.
- Posting Cal/OSHA citations near the relevant work area. Each citation must be displayed until the violation is corrected or for three working days, whichever is longer. Abatement verification documents or tags must also be posted.
- Rectifying cited violations by the deadline given in the Cal/OSHA citation and submitting the required abatement verification documentation.
Falls
Falls are the most common fatal accidents in construction, claiming between 150-200 lives and resulting in over 100,000 injuries annually. For this reason, Cal/OSHA has established guidelines to prevent workers from falling from, onto, or through working surfaces, and to shield them from falling objects.
Employers are required to ensure all work and walk surfaces can adequately support workers. Cal/OSHA mandates that any worker at risk of falling 7 ½ feet or more to a lower level must be given fall protection. This protection can include guardrails, safety nets, personal fall arrest systems (PFAS), positioning device systems, barricades, covers, or a combination. All fall protection systems must meet or exceed OSHA standards and undergo regular inspections by a competent person to ensure ongoing compliance.
Fall protection should be provided in the following situations:
- Exposed sides and edges
- Leading edges
- Hoist areas
- Holes
- Formwork and reinforcing steel
- Ramps, runways, and other pedestrian paths
- Excavations such as wells, pits, or shafts
- Dangerous equipment
- Overhand bricklaying or similar masonry work
- Low-slope roofing work
- Steep roofs
- Precast concrete erection
- Wall openings
- Residential construction
Guardrail Systems
The minimum diameter for top and middle rails should be no less than ¼ inch to avoid potential injuries from cuts or abrasions. If wire rope is used for the top rail, it needs to be visibly marked at intervals not exceeding 6 feet. The top edge height of the top rails or equivalent guardrail system members should measure 42 inches, with an acceptable variance of plus or minus 3 inches above the walking or working level. For situations where there isn't a wall or a parapet wall of at least 21 inches in height, midrails, screens, mesh, or equivalent intermediate structural members should be fitted between the top edge of the guardrail system and the walking or working surface.
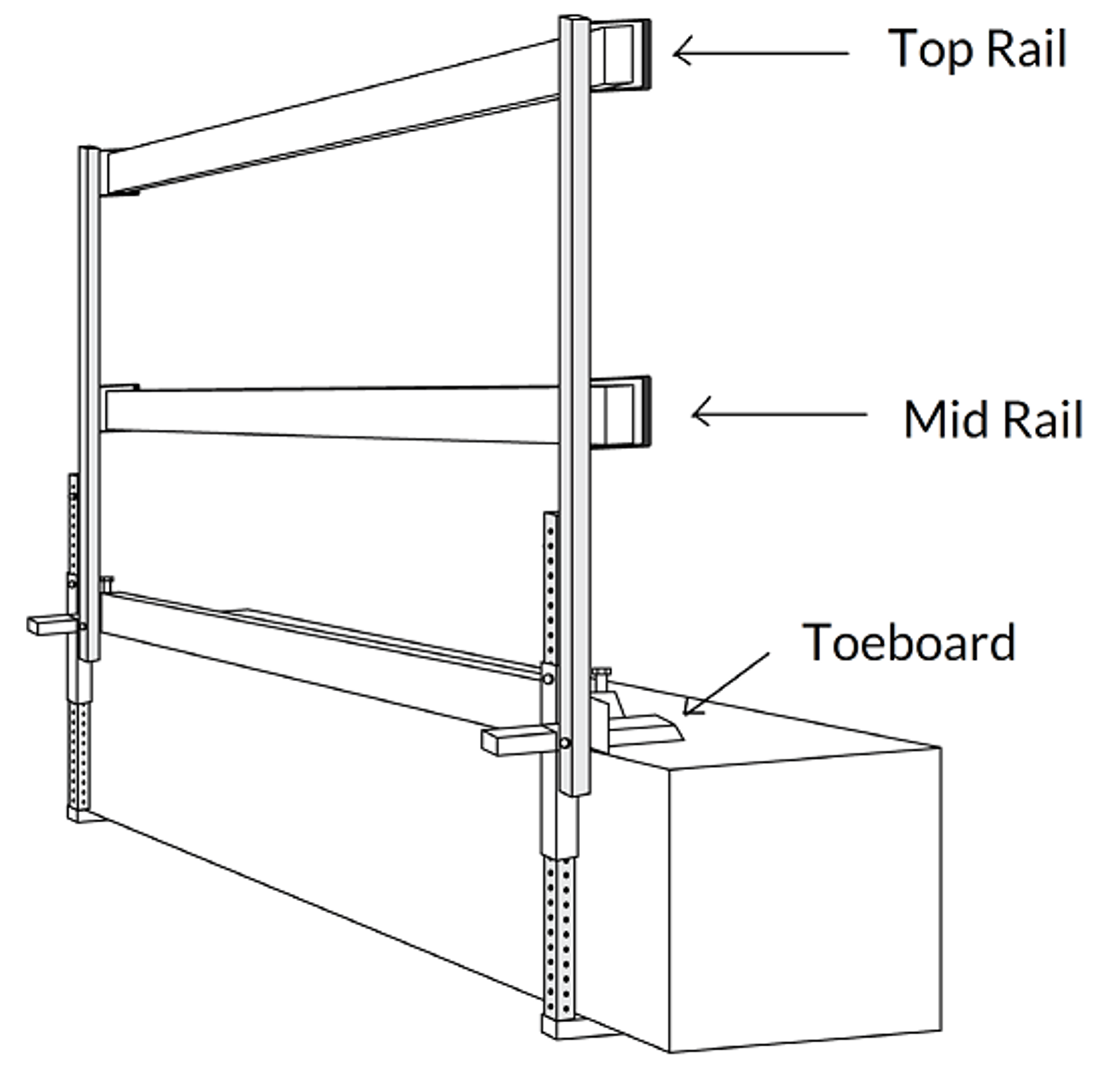
Guardrails and toeboards should be implemented in the following scenarios:
- When the working height is 7.5 feet or more from the ground level.
- On all unenclosed elevated areas like balconies, roof openings, landings, or porches where the working level is more than 30 inches from the ground, floor, or other work areas.
- In places with floor, roof, and wall openings where the wall opening drop exceeds 4 feet and the bottom of the opening is less than 3 feet above the workspace.
- Guardrails with a swing gate or equivalent are required for floor or roof openings that are covered and labeled as "OPENING: DO NOT REMOVE".
Guardrail systems should be designed to withstand an outward or downward force of at least 200 pounds applied 2 inches from the top edge. When the 200-pound force is applied downward, the guardrail's top edge should not deflect to a height less than 39 inches.
Midrails and other equivalent structural members, such as screens, mesh, solid panels, and intermediate vertical members, must be designed to withstand a force of at least 150 pounds applied in any downward or outward direction at any point.
At hoisting areas, a chain, gate, or removable guardrail section should be placed across the access opening between guardrail sections when hoisting operations are not taking place. For holes, guardrails should be installed on all unprotected sides or edges. If the hole is used for material passage, it should only have two sides with removable guardrail sections. When the hole is not in use, it should be covered, or a guardrail system should be installed. If guardrails are used around holes that serve as access points, gates should be used at the point of access to prevent workers from accidentally falling into the hole.
Warning Lines
All sides of roof work zones must be surrounded by warning lines. These systems are made up of chains, wires, or ropes. If mechanical equipment is present, the warning line must be set up at a minimum distance of 6 feet from the roof edge in the direction of the equipment's operation and at least 10 feet from the roof edge perpendicular to the direction of the equipment's operation. Warning lines should be flagged at intervals no greater than 6 feet, should be able to withstand a horizontal force of at least 16 pounds, should have a minimum tensile strength of 500 pounds, and should not tip over when pulled from one end.
Covers
OSHA requires specific standards for covers used to cover holes in roofs, floors, and other work surfaces. All covers should be either color-coded or marked with "HOLE" or "COVER" to serve as a warning. They should be secured upon installation to prevent them from being moved by wind, equipment, or unauthorized personnel.
Covers placed in roadways should be capable of holding twice the maximum axle load of the largest vehicle expected to cross over the cover. All other covers should be able to support at least twice the weight of employees, equipment, and materials.
Personal Fall Arrest System (PFAS)
A Personal Fall Arrest System (PFAS) serves as a critical safeguard for workers, protecting them from incidents of falling. The specific design of a PFAS is aimed at halting a fall while a worker is in the process of descending from a work level. The components of a PFAS include an anchorage point, connectors, and a body belt or harness. It may also include a lanyard, a lifeline, a deceleration system, or a combination of these elements.
Deceleration tools often incorporate a rope grab, and in certain instances, a self-retracting lanyard or lifeline. Snaphooks are one of the most frequently used connectors within a PFAS. The fall protection system can also include a warning line system that warns workers as they approach unguarded sides or edges. It's important to note that as of January 1, 1998, utilizing body belts in a personal fall arrest system is not acceptable. Workers using a body belt as part of a PFAS may face risks such as falling from the belt, sustaining severe internal injuries, or experiencing technical asphyxiation from prolonged suspension.
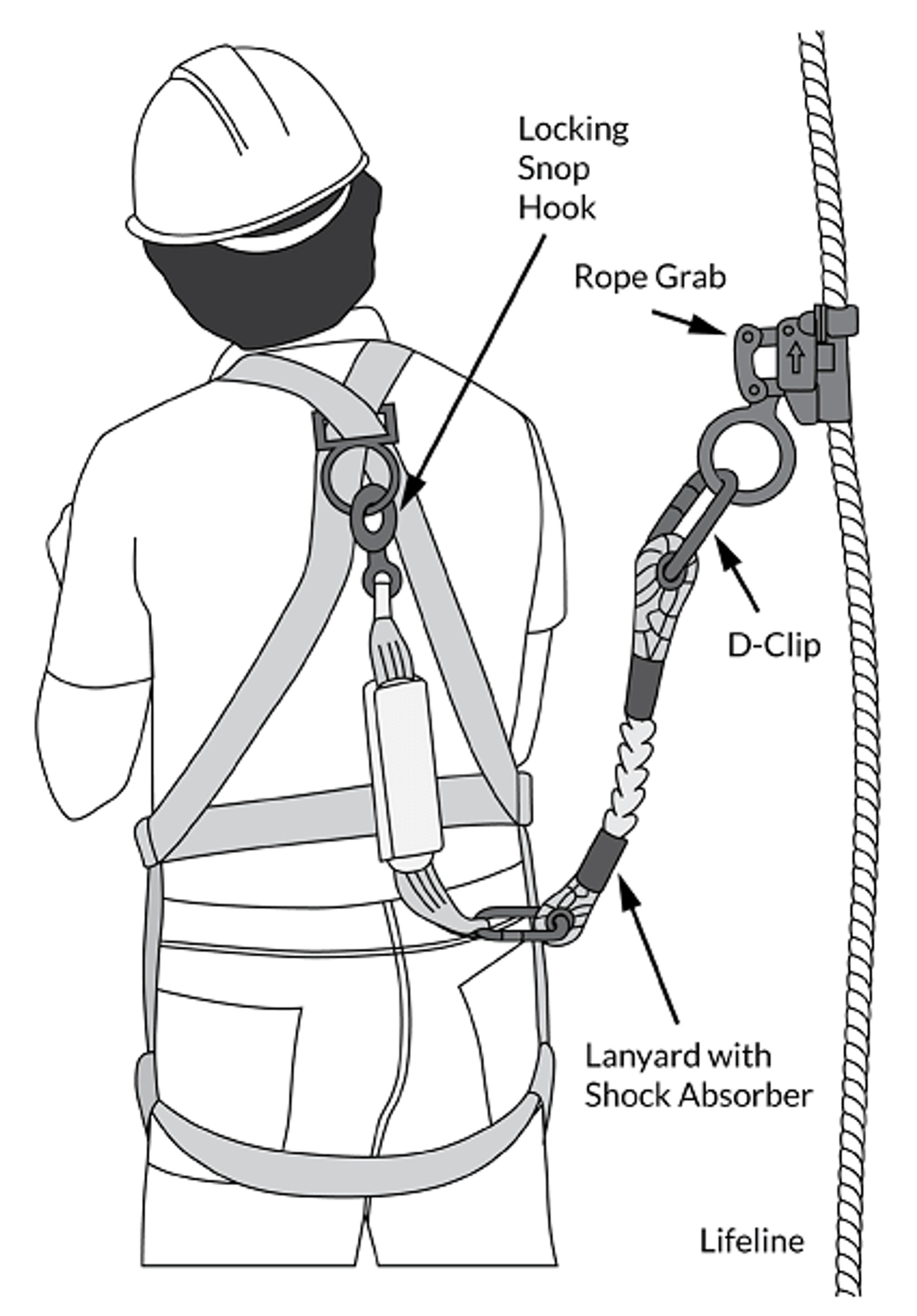
A personal fall arrest system must adhere to the following principles:
- The highest arresting force exerted on an employee when used with a body harness should be capped at 1,800 pounds.
- An employee should not fall over 6 feet or make contact with any lower level
- The system should halt an employee's fall entirely and restrict the maximum deceleration distance an employee travels to 3.5 feet.
- The system ought to have the strength to resist double the potential impact energy of an employee falling freely from a distance of 6 feet, or the free-fall distance the system allows, whichever is shorter.
Safety belts, lifelines and lanyards usage according to Cal/OSHA guidelines stipulates that lifelines should be fastened above the operation point to an anchorage or structural component capable of carrying a minimum dead weight of 5,000 pounds. Lifelines prone to cutting or abrasion should be at least ½-inch wire core manila rope. Safety belt lanyards should be a minimum of ½-inch nylon or an equivalent, with a maximum length that permits a fall of no more than 6 feet.
Safety Nets
When workspaces are positioned over 25 feet above ground, water surfaces, or other areas where the use of safety equipment like ladders, scaffolds, catch platforms, temporary floors, safety lines, or safety belts is not feasible, safety nets should be utilized. Work should not commence until the safety nets are properly installed and tested. Safety nets should be set up to extend 8 feet beyond the edge of the work area where employees are exposed, and they should be placed as near to the work area as possible, never exceeding 30 feet below the work area. In bridge construction scenarios, only a single level of nets is necessary. The mesh size of the nets should not exceed 6 by 6 inches. All new nets must fulfill the minimum impact resistance standards of 17,500 foot-pounds.
Ladder Safety
Ladders are a standard tool in construction work, and their correct usage is crucial for maintaining a safe work environment. The two most common types are stepladders and extension ladders.
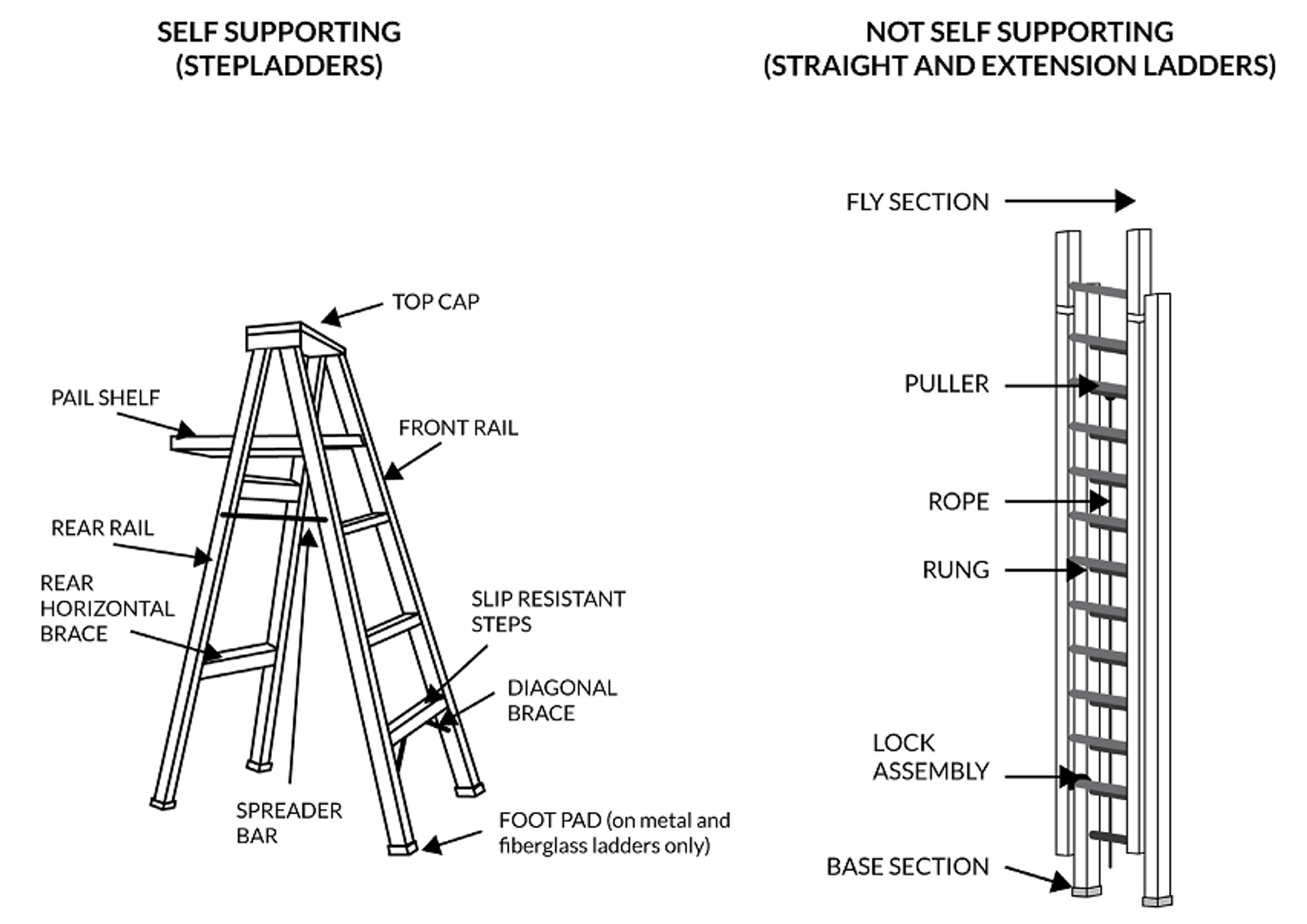
Before utilizing a ladder, familiarize yourself with the manufacturer’s guidelines. Only use the ladder when fully alert and in good health. Avoid using ladders in bad weather or if you're on medication. Steer clear of using ladders in areas with heavy foot traffic or doorways. If a doorway is the only available location, ensure the door is locked. If the door has to remain open or the ladder is elevated, have a colleague secure the area to prevent accidents.
When positioning a ladder, ensure the legs are even and firmly planted on the ground. In case of soft or uneven surfaces, use boards beneath the legs for support. Test the ladder's stability before use. For optimal stability, both sides of the ladder should make contact with a wall or other support. For a stepladder, make sure the legs are fully extended and locked in place. Non-self-supported and extension ladders should be angled at 75 degrees.
Additional safety practices for ladder use include ensuring that hands, shoes and ladder steps are dry before use. It's advisable to have a second person secure the bottom of the ladder and prevent disturbances. Always maintain a three-point grip on the ladder (two hands and one foot or one hand and two feet). Avoid any distractions that could cause you to turn away from the ladder. Climb the ladder slowly and ensure your weight is centered between the side rails. Do not lean back, and never stand on the top two rungs of a stepladder or top three rungs of an extension ladder.
Ladders should be inspected by a competent individual for any signs of damage. Any ladder deemed unsafe should be taken out of service and marked as such. It's also important to match the type of ladder to the specific job. For instance, avoid metal ladders in areas with electrical hazards. Opt for wood or plastic (fiberglass) ladders, which are non-conductive and safer for electrical work.
Employees must refrain from sitting, kneeling, stepping, or standing on the pail shelf, top cap, or the step below the top cap of a stepladder. An employee must not stand and work on the top three rungs of a single or extension ladder unless there are structural members providing a firm handhold or the employee is protected by a fall protection system.
Cal/OSHA categorizes ladders based on the weight capacity they can withstand. The subsequent table illustrates the types of ladders and the corresponding working loads as per Cal/OSHA's classification.
- Light Duty (Type III): 200 lb working load
- Medium Duty (Type II): 225 lb working load
- Heavy Duty (Type I): 250 lb working load
- Extra Heavy Duty (Type IA): 300 lb working load
- Special Duty (Type IAA): 375 lb working load
For the proper use of straight or extension ladders, a good general rule is to place the ladder 1 ft. away from the vertical support for every 4 ft. of ladder height from the base to the top support. The ladder must also extend a minimum of 36 inches beyond the roof's top level or any flat surface.
The following illustration shows the correct usage of an extension ladder:
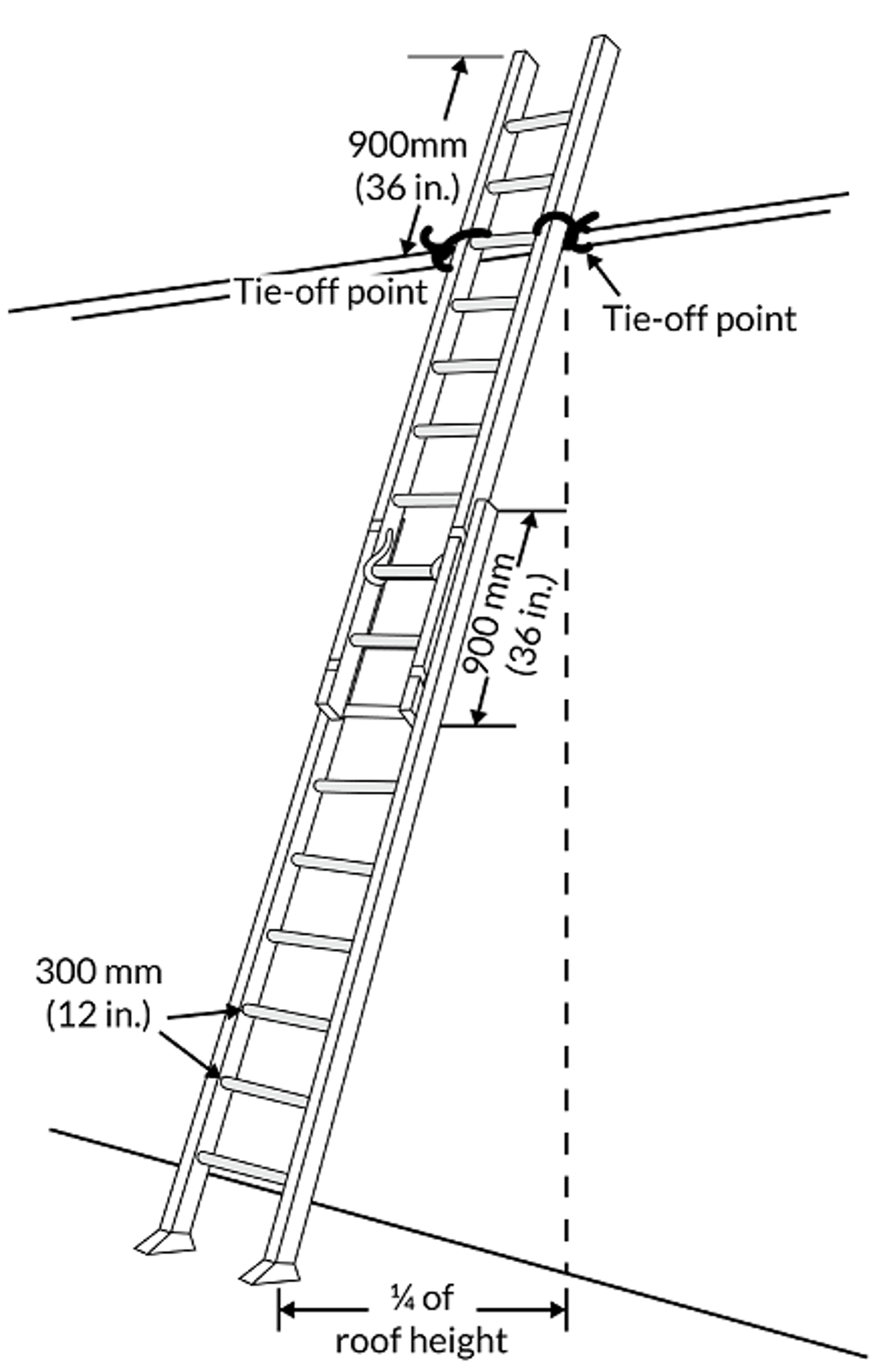
The following is a list of the maximum lengths allowed for various types of ladders at a jobsite:
- Step Ladder: 20 feet
- Extension Ladder with Two Sections (Wood): 60 feet
- Extension Ladder with Two Sections (Metal): 48 feet
- Extension Ladder with Three Sections (Metal): 60 feet
- Extension Ladder with Two Sections (Reinforced Plastic): 72 feet
- Trestle Ladder: 20 feet
- Base Section of Extension Trestle Ladder: 20 feet
- Extension Section of Extension Trestle Ladder: 20 feet
- Step Ladder for Painter’s: 12 feet
- Ladder for Mason’s: 40 feet
- Cleat Ladder: 30 feet
- Ladder for Trolley or Side-rolling: 20 feet
- Single Ladder: 30 feet
For two-section extension ladders, the overlap between sections must be no less than the following lengths:
- Ladder Size: Up to and including 32 feet
- Minimum Overlap: 36 inches
- Ladder Size: Over 32 feet, up to and including 36 feet
- Minimum Overlap: 46 inches
- Ladder Size: Over 36 feet, up to and including 48 feet
- Minimum Overlap: 58 inches
- Ladder Size: Over 40 feet, up to and including 60 feet
- Minimum Overlap: 70 inches
Safety and Types of Fire Extinguishers
Fire extinguishers come in a variety of shapes and sizes, and each one is designed to put out a specific type of fire. They are meant to extinguish small fires, not large, uncontrollable ones. It's essential to use the right type of extinguisher for the specific fuel burning in the fire, as using the wrong one can exacerbate the situation. The National Fire Protection Agency (NFPA) classifies fires based on the type of fuel they burn, and the most common types of fire extinguishers are designed to combat these classifications.
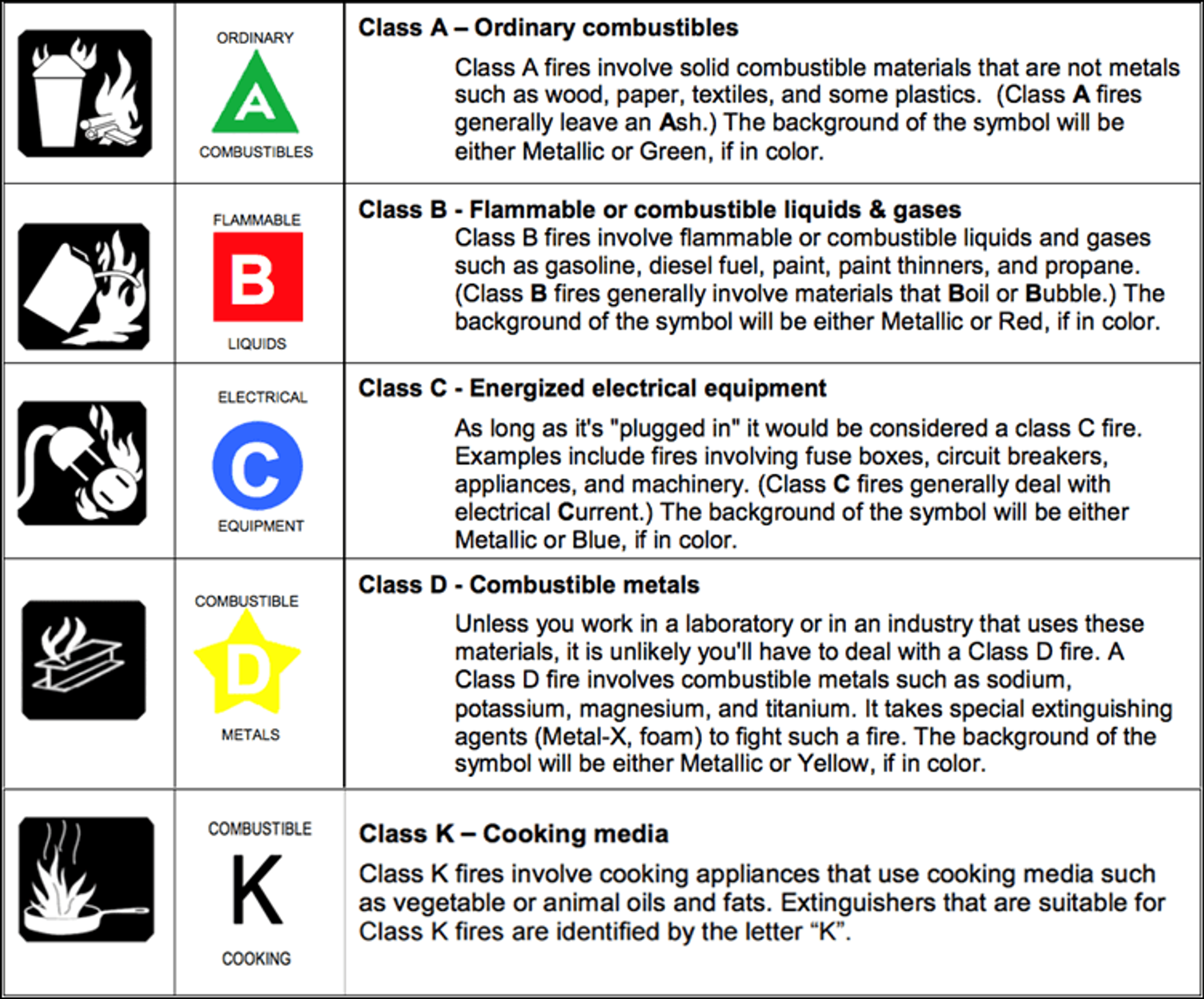
It's crucial to understand the types of fuels when selecting the appropriate fire extinguisher for a particular situation. Here are the four different kinds of fire extinguishers:
- APW (Water): This type is specifically designed for Class A fires.
- CO2 (Carbon Dioxide): This extinguisher is suitable for fires classified as Class B & C.
- Dry Chemical (ABC, BC, DC): ABC indicates that the extinguisher can be used for Class A, B & C fires. BC denotes that it's for Class B & C fires. DC stands for Dry Chem.
- Wet Chemical: This extinguisher is effective against Class A, C & K fires.
When using a fire extinguisher during an emergency, it's crucial to be positioned near an exit, allowing for a quick escape if the fire becomes uncontrollable. Most portable fire extinguishers provide 15 to 30 seconds of continuous usage. Therefore, planning an escape route is essential. Also, it's generally recommended to maintain a distance of 20-30 feet from the fire for safety.
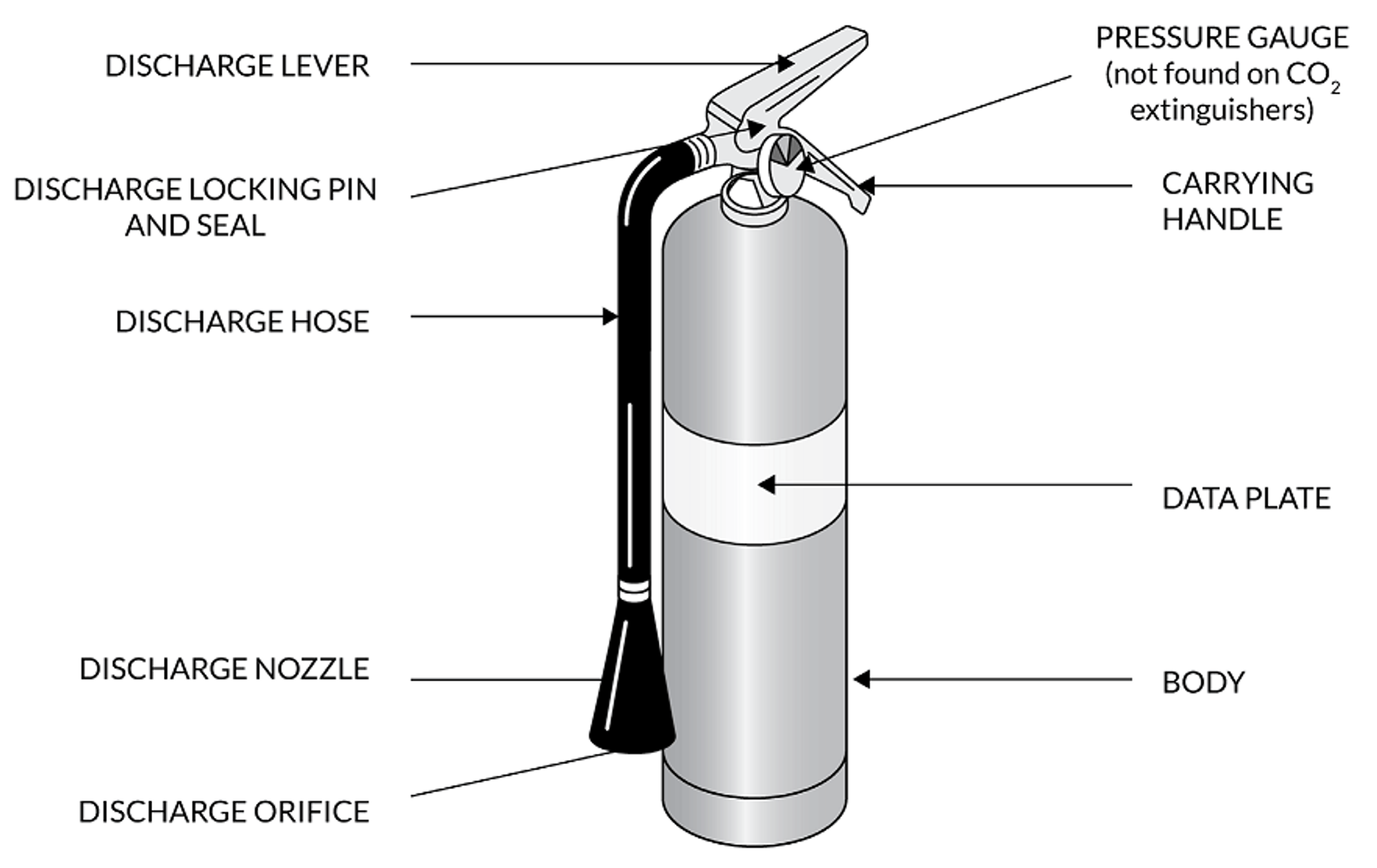
Using a fire extinguisher can be broken down into four easy steps (PASS):
P - Pull the pin to disable the safety mechanism and activate the fire extinguisher.
A - Aim the fire extinguisher at the fire's base.
S - Squeeze the trigger while holding the extinguisher upright.
S - Sweep the extinguisher from one side to the other, making sure to cover the fire area. Repeat if the fire rekindles.
Asbestos
Whenever a contractor plans to perform asbestos-related tasks, they must inform DOSH 24 hours before the work begins, regardless of the amount of asbestos-containing material that will be disturbed. The written notification must be submitted to the nearest Cal/OSHA district office. In cases where immediate abatement is required, verbal notification can be given but must be followed by written confirmation within the next 24 hours.
Any employer or contractor who disturbs more than 100 square feet of asbestos-containing construction material (containing more than 0.1 percent asbestos by weight) at a single worksite must register annually with the Asbestos Contractors Registration/Occupational Carcinogen Control Unit.
Any person who offers consulting services related to asbestos-containing construction material exceeding 100 square feet must be certified. The Asbestos Consultant and Trainer Approval Unit provides certification to qualified individuals.